Gratowanie
Jak usunąć ostre krawędzie blach
Gratowanie jest to proces, podczas którego usuwana jest ostra pozostałość z krawedzi detalu, zwana gratem lub zadziorem, pojawiająca się w czasie różnego rodzaju obróbki.
Podczas produkcji nie można uniknąć powstawania ostrych krawędzi i innych niedoskonałości. Są to w dużej mierze produkty uboczne cięcia laserowego, cięcia strumieniem wody, wykrawania, wypalania plazmą czy gazem. Utrudniają one kolejne procesy produkcji. Jest to również warunek wstępny dla innych procesów, nie wspominajac o bezpieczeństwie i estetycę.
Korzyści gratowania to:
- Minimalizowanie ryzyka urazu:
- Dla pracowników podczas transportu i montażu części
- Podczas użytkowania i/lub naprawy produktu - Poprawa jakości powierzchni dla kolejnych procesów(np. malowanie proszkowe czy cynkowanie).
- Zgodność z normami
- Poprawa estetyki wyrobów
Metody gratowania:
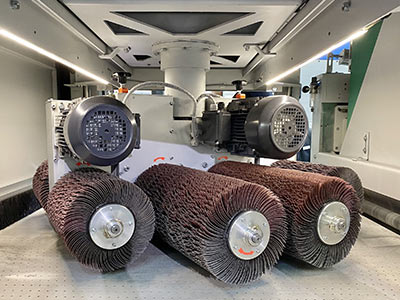
Gratowarka LOEWER RotoMaster
Obróbka maszynowa wykorzystuje maszynę do szlifowania i gratowania zadziorów. Ta metoda jest droższa, ale znacznie wydajniejsza niż ręczne gratowanie, staje się ona coraz bardziej popularna.
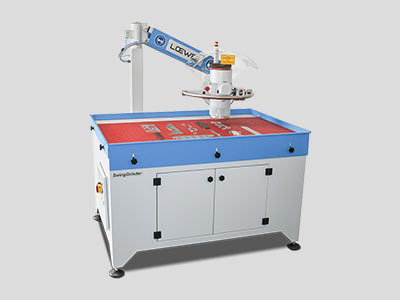
LOEWER SwingGrinder
Istnieje również opcja maszyny półautomatycznej, który wypełnia lukę pomiędzy pracochłonnym ręcznym gratowaniem a drogimi automatycznymi szlifierkami szerokotaśmowymi. np. SWING GRINDER firmy Loewer.
Producenci gratowarek szerokotaśmowych oferują różne konfiguracje maszyn zbudowanych z modułów/agregatów. Mogą one mieć postać pasów, dysków, walców czy segmentów.
Główni producenci szliferek szerokotaśmowych na polskim rynku to: Costa, Ernst, Fladder, Lissmac, Loewer, Madora, NS Máquinas, Q-Fin, RWT, Timesavers, Weber
Etapy gratowania
Usuwanie żużla
Podczas cięcia plazmą i gazem często dochodzi do topienia się materiału, a po stronie strumienia pojawia się stopiony metal, tak zwany żużel, którego usunięcie jest niezbędne do dalszej obróbki.
Powszechnie stosowane ręczne metody usuwania żużla to skuwanie za pomocą młota i dłuta lub szlifowanie za pomocą szlifierki kątowej. Nadmiar przywartego materiału można usunąć poprzez szlifowanie miękkim walcem kontaktowym. Jednak najbardziej skuteczną metodą odbijania żużla jest obróbka mechaniczna z zastosowaniem dysków zbudowanych z młoteczków. Młoteczki te odbijają pozostały żużel z detali nie dotykając ich powierzchni. Ten proces znajduję zastosowanie przed szlifowaniem wstepnym.
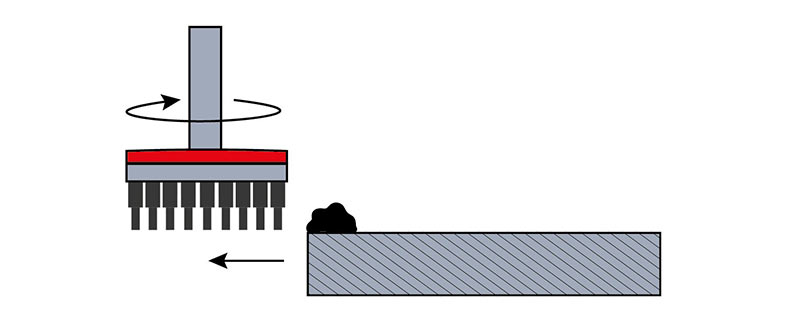
Szlifowanie wstępne i gratowanie
Grat lub też grat pierwotny to nagromadzenie się materiału na obrabianych detalach, które wystają ponad ich krawędzie i powierzchnie. Szlifowanie wstępne z reguły usunie grat pierwotny, odpryski, nierówności i/lub pozostałe warstwy zgorzeliny przygotowując detal do kolejnego etapu obróbki.
Główną wadą szlifowania wstępnego jest to, że chociaż doskonale radzą sobie z usuwaniem zadziorów pionowych, mają tendencję do toczenia nadmiaru materiału po krawędziach przedmiotu obrabianego w celu utworzenia zadziorów bocznych czyli tzw. grat wtórny. Przy usuwaniu gratu podstawowego kładzie się nacisk na jak największą redukcję powstawania gratu wtórnego, ma to na celu zwiększenie jakości i efektywości obróbki detali oraz ochronę i wydłużenie żywotności narzędzi służących do usuwania gratu wtórnego i zakraglenia krawędzi.
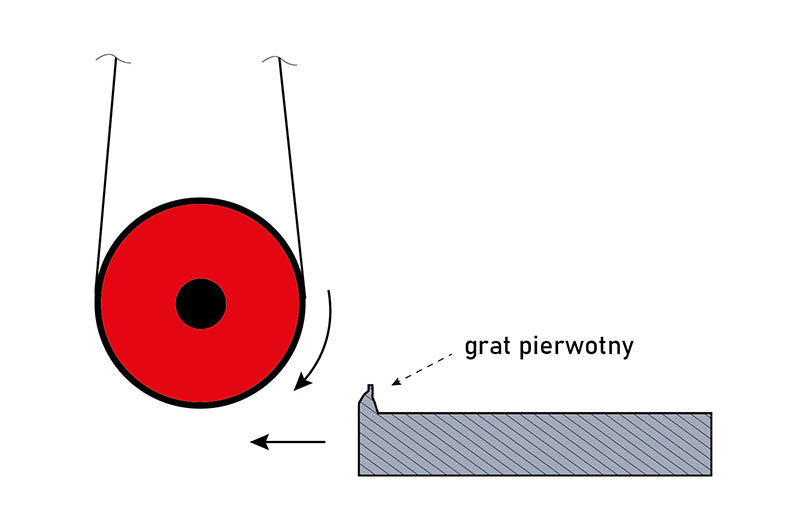
Gratowanie i zaokrąglanie
Podczas tego procesu następuje usunięcie pozostałego gratu pierwotnego oraz gratu wtórnego, a także zaokrąglenie krawędzi. Aby stworzyć warunki do kolejnych kroków obróbki (malowanie proszkowe, lakierowanie, itd.) oraz wykluczyć niebezpieczeństwo zranienia ostrymi krawędziami, usuwanie gratu łączy się często z zaokrąglaniem krawędzi. Promień zaokrąglenia sięga od dziesiątych części milimetra do ponad dwóch milimetrów.
Gratowanie i zaokrąglanie krawędzi wykonuje się za pomocą elastycznych narzędzi ściernych umożliwiających dobre dopasowanie do wewnętrznych i zewnętrznych konturów blach oraz do otworów i wycięć. Dlatego w urządzeniach ręcznych oraz maszynach do szlifowania i gratowania stosuje się odpowiednie tarcze szlifierskie, walce, dyski, segmenty czy szczotki. Maszyny do gratowania wyposażone są również w system głowic planetarnych lub agregaty oscylacyjne służące do równomiernej obróbki krawędzi.
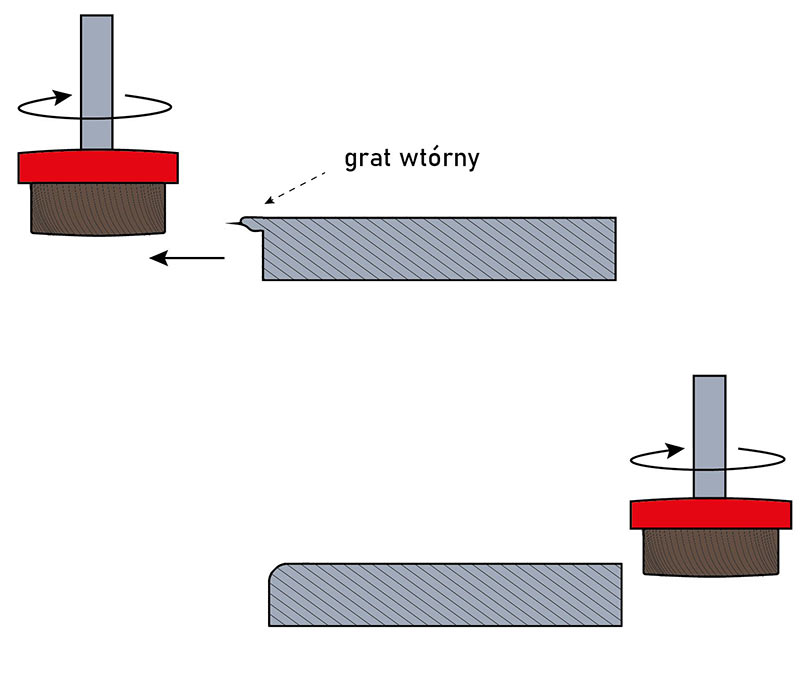
Szlifowanie wykańczające
Ten etap procesu ma na celu zeszlifowanie śladów porysowania oraz stworzenie powierzchni o estetycznym wyglądzie. Krok ten pozwala na osiągnięcie określonych struktur szlifu na powierzchni blachy.
Korzyści gratowania z użyciem szlifierek szerokotaśmowych
- Zwiększenie bezpieczeństwa: Korzystanie z maszyny do gratowania sprawi, że proces będzie bezpieczniejszy od początku do końca. Dla operatorów automatyzacja eliminuje potrzebę przebywania w strefie pracy i minimalizuje ryzyko urazów związanych z powtarzalnym ruchem. Elementy pozbawione ostrych pozostałości są również bezpieczniejsze w obsłudze po ich wykończeniu.
- Poprawa spójności: Automatyzacja procesu oznacza, że jakość nie będzie się różnić między operatorami i ograniczy ilość poprawek, które musi się wykonać.
- Wyższa jakość wykończenia: gratowanie elementów za pomocą maszyn poprawia ostateczną jakość produktu.
Viktor Puček - KPL Trading sp. z o.o.
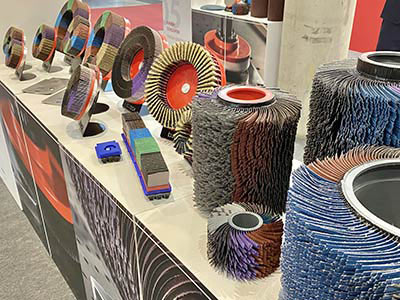
Dyski i walce do gratowania
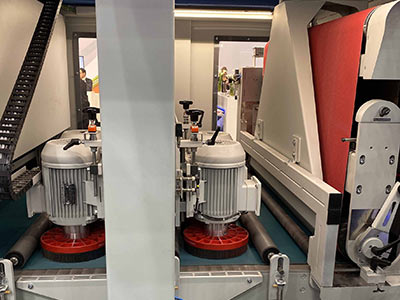